in 1912, but the first real success, with methane over a nickel catalyst, came in the 1920s. It wasn't commercialized until 1931. (Smil 113). Note that the reforming catalyst isn't necessarily the simple metal; the 1962 ICI process used nickel-potassium oxide-aluminum oxide (Weissermel 18).
In the 1632 universe, the likeliest source of the volatile hydrocarbons would be coal gas, but natural gas would also be an option. However, we do have to find the right catalyst, and the feedstock may include substances (sulfur, chloride) that poison the catalyst.
Immediately prior to the RoF this was the dominant method of producing hydrogen. the
CH3OH-›CO+2H2.
Steam reacts with the carbon monoxide to form carbon dioxide and more hydrogen. The process has been proposed for modern field use, with a one ton trailer-mounted generator producing 150 cubic feet/hour with fuel consumption of just over one gallon/hour. (Philpott).
In the old time line, it had higher operating costs but lower fixed costs than the hydrocarbon-based scheme. (Blomen, 150). Other advantages are that methanol is free of sulfur and the reaction can be run at a lower temperature (300°C). (Liu 65). However, the problem is that experimentation will be needed to find appropriate catalysts (likely to be copper, zinc oxide or palladium-based).
****
If the reagents are stored close together, and their containers are ruptured, an uncontrolled reaction can occur.
Some of the reactions are exothermic, so even if the reaction is in the proper vessel, the temperature has to be monitored.
I was able to find some comparative operating cost data on the different production processes. Some sources include labor and overhead (interest and depreciation on fixed costs), and others don't.
Figure that one 1900 US dollar is 4.2 contemporaneous British shillings, or 0.5 1632 shillings if deflated based on Allen's laborers' wage rates, and 1.25 if using Allen's London CPI. (Two shillings is equivalent to one Dutch guilder. ) That same 1900 dollar is $19.57 in 2000 if inflated using the Sahr CPI.
The NTL economy in 1635 is going to be very different than that of pre-RoF Europe, and also different from that of OTL early-twentieth century Europe. Hence, be cautious about putting a lot of faith on cost conversions. It's probably better to use the table to get a sense of relative rather than absolute costs, but even that's dangerous; individual inputs (e.g., electrical energy) could be cheaper or more expensive in the new universe, even different from one region to another.
It's interesting to note that, depending on who you ask, electrolytic hydrogen is cheaper (Roth), more expensive (Ellis/Sander), or the same cost (Greenwood) as hydrogen from the steam-iron plant. I suspect that it turns on what the assumed cost of power is. Bear in mind that nowadays, electrolytic hydrogen is much more expensive than hydrogen from steam reforming.
This cost data (Tables 5A, 5B) is not available in Grantville, but they can calculate the materials requirements and cost them out separately.
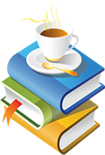
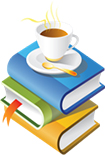
(1) materials only, steam and water treated as free; refrigeration power cost of 60 cents/1000cf.
(2) Ellis 595, mostly based on Sander; additional prices of 18.75 for silicol (p523) and 32-38 for hydrogenite (521ff). Cp. 462ff for fractional refrigeration, 445, 458 for Griesheim-Elektron 472 Carbonium.
(3) Greenwood 213, 234. Assumes power cost of 0.25p/kwh.
Ellis (537ff) breaks down the operating cost for electrolytic production of 632 cubic feet compressed hydrogen/hour (4,550,400 cubic feet/year of 300 workdays, 24 hours/day) and half that of compressed oxygen as follows:
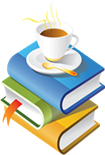
I talked about purification of carbon monoxide in the section on 'water gas.' In essence, carbon monoxide may be removed by treatment with cuprous chloride, or hot soda lime, caustic soda, or calcium carbide, or by liquefaction. Carbon dioxide is eliminated by washing with slaked lime, or water under pressure. Bog iron ore will extract hydrogen sulfide. (Greenwood 211ff).
Generally speaking, in the early-twentieth century, hydrogen was compressed for shipment to industrial customers. In 1904, figure that a gas compressor for compressing 100 cubic meters of hydrogen every 10 hours cost $1000, and a second compressor for the associated 50 cubic meters oxygen would be $625. (Engelhardt 39). Ellis (556) estimated that compressors for a 10 cubic meter/hour hydrogen system would be $2850.
According to Ellis (538), an electrolytic hydrogen plant would require 4 kilowatt-hours for compression of 632 cubic feet (17.9 cubic meters) hydrogen to 300 psi (20 atmospheres), and 12 kilowatt-hours to compress 316 cubic feet oxygen to 1800 psi. Engelhardt (113) says that for compression to 100-120 atmospheres, the total power required would probably be about 4 kwh for 1 m3 hydrogen and 0.5 oxygen.
The tanks were also a significant expense. The plant had to purchase enough so that it didn't have to wait for empties to be returned in order to keep up with demand. The steel tanks weighed 10 kilograms per cubic meter gas held, and a 40 kg tank cost $11.75 in 1904. (Englehardt 118ff).
You have to be careful; don't use the same compressor alternately for hydrogen and oxygen, and don't use a former oxygen cylinder to carry hydrogen, or vice versa, without being sure that you completely removed the old gas. (Ellis 592).
****
An alternative to compression is liquefaction. Hydrogen was first liquefied in 1898. Liquefaction requires bringing the hydrogen to a pressure above its critical pressure (12.8 atmospheres), and then cooled below its critical temperature (-239.95oC). Keeping it liquid requires keeping it pressurized and cold, even in transport. And if you fail, well, remember that liquid hydrogen is a rocket fuel. I think it will be decades before liquid hydrogen appears in the new time line.
****
Since military balloons had to be launched near the front line, where transportation options were likely to be limited, the tanks were moved by a variety of means. The first use of compressed hydrogen in warfare was possibly in the British expedition to the Sudan (1885); each camel carried two 66 pound cylinders, each carrying 140 cubic feet (after expansion) of gas. (AGLJ) In the Boer War, fifty horses were needed to transport cylinders (weighing 1