для серийного производства, реализовали 568 конструктивных улучшений, внедрение которых позволило снизить вес самолета на 120 кг, повысить его гарантийный ресурс на 100 часов, сократить время на предполетную подготовку на 35 мин., а к повторному вылету – на 25 мин. Снизились на 34 чел/час и трудозатраты в эксплуатации.
Освоение МиГ-25 предрешило техническую революцию на предприятии.
Практически во всех цехах, связанных с изготовлением баковых отсеков фюзеляжа и крыла, пришлось организовывать и изучать с нуля сварочное производство (до этого самолеты были клепанными), обучать рабочих, конструкторов, технологов новым профессиям. В конструкции планера МиГ-25 сварка стала основным типом неразъемных соединений. При изготовлении агрегатов самолета использовались все виды сварки как высокопрочных сталей, титана, так и алюминиевых сплавов. При этом контактная сварка заняла лидирующее положение. Конструкторам пришлось осваивать новые приемы конструирования сварных агрегатов планера, используя тонколистовые материалы из стали и титана.
Ранее других агрегатов запускался в производство баковый отсек фюзеляжа, как наиболее сложный. Общее мнение руководства завода формулировалось так: 'Будет баковый отсек – будет самолет'.


О том, как проходило освоение МиГ-25 вспоминает заместитель главного директора ОАО 'Нижегородский авиастроительный завод 'Сокол' В.П. Люльков, в те годы мастер агрегатно-сборочного цеха 9:'… Для всего инженерно-технического состава это была новая работа, ранее мы знали и использовали при сборке самолетов преимущественно клепку и металлы на основе AI и Мд. При создании МиГ-25 осваивалась новая технология – сварка конструкции из высокопрочных стальных и титановых сплавов. Перед цехом 9, который специализировался как раз в этой области, стояла сложная задача – научиться варить такие фюзеляжи. В то время рабочий график с 7 часов утра и до 7 вечера был нормой. Я помню, когда производственные совещания в цехах 9 и 21 назначались на 9 или 10 часов вечера, а вместо этого, в силу производственной необходимости проводились даже в 12 часов ночи. А в 7 утра уже надо было быть опять на работе.
Не все выдерживали, но жить было интересно. Тогда вполне нормальным явлением было, когда по субботам на завод приезжал министр авиационной промышленности П.В. Дементьев, который хорошо знал не только директоров заводов, главных инженеров, но и начальников цехов. Как правило, для решения вопросов с ним приезжали главный конструктор А.И. Микоян, РА. Беляков, ставший впоследствии Генеральным конструктором ОКБ им. А.И. Микояна, профессора, академики.. Если не получалась подгонка люков или сварка, они на месте совместно с заводскими рабочими, инженерами и конструкторами решали проблемы. Конечно, общение с людьми такого уровня, корифеями авиационной науки и техники, давало людям возможность подняться на новую высоту'.
После тщательной проработки было сформулировано множество серьезных предложений по улучшению конструкции, которые были сведены в комплекс мероприятий и одобрены министром авиационной промышленности П.В. Дементьевым. Производство баковых отсеков фюзеляжа было организовано в старом корпусе сборки 72. Он последовательно заполнялся стапелями сборки рам, шпангоутов, отсеков, причем в подавляющем большинстве стапеля выполнялись поворотными и совмещали в себе функции сборочного приспособления и манипулятора. Группы стапелей объединялись в специализированные линии и участки. Для производства цельносварных самолетов потребовалось оборудование по надежности на несколько порядков выше выпускавшегося в то время промышленностью. И поэтому, по техническому заданию Горьковского авиазавода, две ленинградские организации – Всесоюзный институт электросварочного оборудования и завод 'Электрик' Министерств электротехнической промышленности – занялись разработкой и изготовлением сварочных машин на новой элементной базе, надежность которых была во много раз выше прежней. На эту работу потребовалось около десятка лет. В итоге завод приобрел и внедрил в производство такие машины как: МШВ-1601, МТВ-2001, МТВР-4001, МТ- 1223. Они позволили получить сварные соединения стабильные по качеству сварных швов.
Во внедрении новых сварочных процессов и оборудования активное участие принимали инженеры: A.M. Никитинский, С.Е. Ушакова, Р.П. Пацельт, В.А. Каманин, М.Д. Бойко, А.С. Рытов.
К новым технологическим процессам необходимо отнести и многоимпульсную штамповку взрывом листовых деталей из высокопрочных нержавеющих сталей. Во внедрении этих процессов принимали участие инженеры Ю.А. Веселков, Ю.Ф. Храмов, В.Н. Короткое.
Серийное поточное производство самолетов МиГ-25 налаживалось в новом корпусе 103. Была поставлена задача резкого сокращения трудоемкости монтажно-сборочных работ, в решении которой приняли активное участие конструкторы ОКБ Горьковского авиазавода. Главный конструктор Е.И. Миндров учил своих конструкторов критически и творчески рассматривать каждую деталь, узел, отсек с точки зрения трудоемкости, веса, ресурса и удобства в эксплуатации. Он бывал очень недоволен, если они обращались за каким-либо конструктивным решением непосредственно к микоя- новцам, и требовал от них самим разрабатывать и просчитывать это решение, а в Москву представлять только на утверждение. 'Мы хозяева самолета, и все вопросы должны решать мы, а для микояновцев серийный самолет это пройденный этап, и не надо мешать делать новую технику', – так требовал Евгений Иванович.


Конструкторов Горьковского ОКБ нередко привлекали в Москву помогать проводить технологическую проработку чертежей новых самолетов. Вот и при разработке чертежей на МиГ-25 большие группы Горьковских конструкторов месяцами находились в командировках и помогали микояновцам. Это была неплохая школа взаимного творчества.
Многие разработки Горьковских конструкторов по МиГ-25 являются уникальными и защищены авторскими свидетельствами. Так, С.И. Тимофеев изобрел 'плавающую' гайку для стыка крыльевых отсеков. Были предложены и другие конструктивные решения: 'мертвые болванки' противофлаттерных грузов на концах крыла были заменены на азотные баллоны высокого давления, был упрощен и облегчен носок закрылка путем снятия элементов системы сдува пограничного слоя, на аэродинамическом гребне крыла были введены закрытые разрезы-компенсаторы на всю высоту гребня, на открытых подшипниках тяги закрылка установили защитные элементы, был разработан усиленный зализ крыла, прежний в эксплуатации разваливался от 'сапожных' нагрузок при обслуживании самолета (на зализ часто наступали), усилили верхушки килей самолета, которые трещали от больших вибраций в полете. Эти работы выполняли конструкторы Л.Н. Зингаев, Б.Н. Шмонин, З.М. Коровина, Т.Е. Кузолева, А.Е. Редкозубова, С.Д. Лукьянчук, С.Ю. Ишаева, Л.И. Балашов.
В конструкции МиГ-25 и его модификациях нашли широкое применение тонколистные стрингеры из высокопрочных нержавеющих сталей и сплавов титана, изготавливаемые холодным формированием на трехвалочных станках.
Освоение в производстве МиГ-25 стало локомотивом ускорения научно- технического прогресса на заводе, меняло его организационную структуру. В 1966 году была создана лаборатория комплексных испытаний для проведения входного контроля сложных систем и комплексного бортового радиоэлектронного оборудования, а также для проверки функциональных связей входящих изделий и их комплексиро- вания перед выдачей в цех сборки.
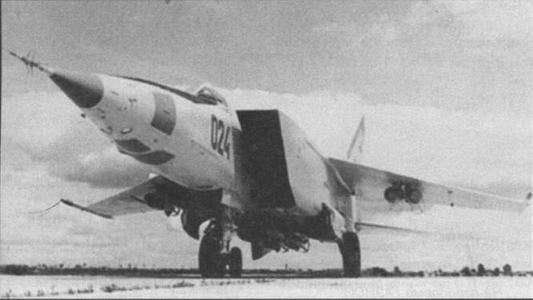